Revolutionary Waste-to-Energy Innovation by Bellwether Technologies
With over 30 years of expertise, Bellwether Technologies (BWT) has mastered the art of gasification-based waste-to-energy plants, paving the way for a cleaner and sustainable future.
IMRG Technology: Transforming Waste into Clean Fuel
Versatility and Advantages
IMRG technology is applicable across all sectors where energy is generated, offering unparalleled advantages:
Versatility and Advantages
IMRG technology is applicable across all sectors where energy is generated, offering unparalleled advantages:
- High availability and flexibility with raw materials, treating various waste types without pre-treatment.
- A recuperative closed-loop process with minimal ecological impact.
- Reduced environmental impact through the generation of clean fuel.

Innovative Process Organization
Tested in large-scale units, our new process organization perfectly aligns with requirements. Noteworthy features include recuperative conversion at high temperatures, transforming residual carbon into synthetic gas, and processing inorganic residuals into inert slag. The resulting gas undergoes thermal treatment in a high-performance reactor with plasma conditioning, annihilating all organic toxic compounds.
Key Features of Our Technology:
- Efficient energy recovery from a wide range of waste in a compact plant, minimizing space requirements.
- Highly efficient and environmentally friendly processes with top-notch operational safety.
- High-temperature processes ensuring the destruction of all toxic substances.
- Production of inert slag suitable for valuable construction material.
- Recovery of metals and minerals as valuable products.
- High-temperature plasma treatment and advanced gas cleaning system generating clean, valuable fuel to substitute fossil fuels.
- The produced clean gas can be used as fuel or energetically in co-generation which is the most advantageous application
- Emissions are below the strictest requirements in Europe and international standards. Dioxins and furnaces are completely decomposed.
- Low investment, maintenance and operating cost leads to a high economy and to an attractive return on investment.
Waste as Feedstock: Utilizing Caloric Resources
The IMRG process excels in utilizing caloric resources from various input materials:
- Biomass and agricultural residuals
- Municipal Solid Waste (MSW)
- Industrial waste (e.g., car tires)
- Hazardous waste
- Refuse Derived Fuel (RDF)
- Caloric feedstocks for quality improvement
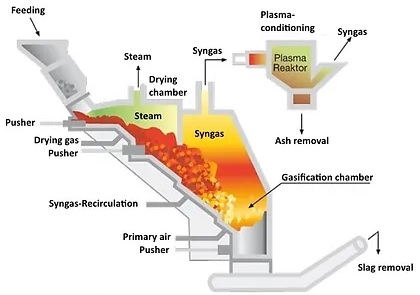
Four-Step Recuperative Process Unit:
- Material hopper unit for continuous waste feeding
- Drying chamber using recovered heat for dehumidification
- Gasification chamber with oxidation and reduction zones
- Bottom discharge for slag or ash removal
Thermal After-Treatment with Plasma Conditioning:
A crucial component of the IMRG process is the thermal after-treatment of syngas through plasma conditioning, vital for cracking and transforming macromolecular hydrocarbons. This process is carried out in a compact unit, the plasma reactor, encompassing a plasma torch, mixing zone, reaction and sedimentation zone, and fly ash.
Purity Ensured through Wet Gas Scrubbing:
Substituting natural gas or combustion in high-efficiency gas engines requires high syngas purity, achieved through wet gas scrubbing. The IMRG process produces only 30% of the gas volume of conventional incineration plants, leading to significantly reduced pollutants and gas cleaning expenditures.
Energy Recovery and Sustainable Transformation:
Our plant can recover almost 90% of the waste’s energy content, transforming it into high-quality syngas and heat. Recycled metals serve as high-quality raw materials for the metal industry, while the inert and vitrified slag finds use in construction.
Join Us for a Cleaner World!
Contact us for more information and become a part of the sustainable future. Together, let’s make a cleaner world a reality!